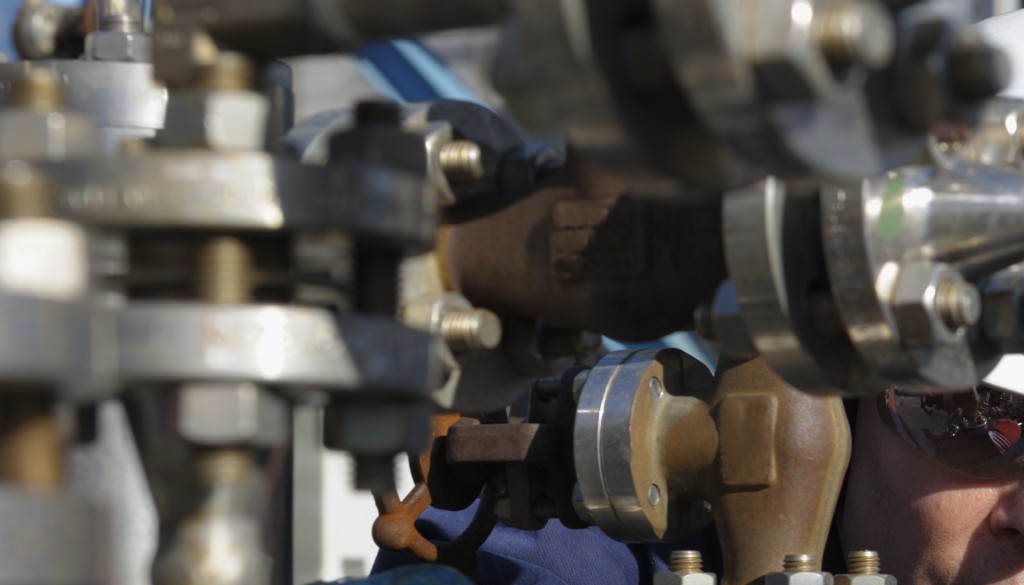
Real-Time Analysis in Chemical Processing
Chemical processing and other batch manufacturing operations are becoming increasingly complex. Manufacturers today need to have a fast response time when quality issues arise and when equipment requires maintenance. Combining real-time analysis with reliability-centered maintenance is a great way to raise efficiency in chemical processing. A constant stream of data coupled with a proactive maintenance plan can ensure that production quality remains high and that plant assets operate in prime condition.
Real-Time Analysis Improves Product Quality
Chemical Processing explained that in batch manufacturing operations, identifying product quality deviations is not an easy thing to do. Additionally, if production continues, and quality issues are not spotted, the cost of wasted time, materials, and energy adds up quickly. This is why it is beneficial to use predictive control techniques so that product quality remains consistent.
According to Chemical Processing, product quality checks should be done with high frequency and accuracy. Automated feedback control can help manufacturers keep track of operations. However, measurements need to be taken without interrupting processes or increasing risk of contamination. Off-line, at-line, and on-line automated devices can allow measurements to be taken close to the process without slowing down the pace of production. Manufacturers can leverage these technology solutions to minimize or even eliminate time delays, if they are able to use the steady stream of accurate and reliable information.
“Product quality checks should be done with high frequency and accuracy.”
Analyzers will provide measurements in real-time or near-real time to manufacturers, but they must be able to respond quickly. For that to happen, KPIs from the analyzers should be worked into the management operating system so that plant managers know how to respond to spikes or dips in the numbers. Data is only useful if companies know how to use it. This is why manufacturing industry experts pride themselves on having a hands-on approach, because giving consulting advice from the boardroom is not always helpful.
Use technology to provide real-time analysis to monitor quality
Data Helps Manufacturers Stay Competitive
Chem.info explained that big data is changing the chemical industry in a profound way. Companies can real-time analysis data from production centers to increase margins, improve product quality and shape business processes. Once manufacturers put the systems in place that collect the data, they should then identify the best ways to use the data to reduce costs, manage assets, generate revenue, and make smarter decisions going forward. Plant managers who can effectively interpret the data and respond accordingly will see noticeable improvements in their business. For example, data analysis can help manufacturers make variants of existing products and either lower production cost per unit or produce a higher quality substitute with higher profit margins.
One practical way to use data from real-time analysis is to link it with reliability-centered maintenance. Demonstrating vigilance in monitoring quality and production levels, as well as keeping assets in optimal condition, can lower overheads and raise efficiency. As previously mentioned, the chemical manufacturing process is complex, but properly leveraging data makes things simpler, allowing companies to better manage production assets and throughput processes simultaneously.
It is important to mention, however, that smart technology alone will not provide the desired benefits. Data collection and analysis is only a means by which better decisions and actions are taken. Companies that understand this last point know that educating staff on how to interpret and proactively respond to KPIs is equally as important as investing in new technology. As the manufacturing field continues to be influenced by evolving technology, management skills must evolve as well.