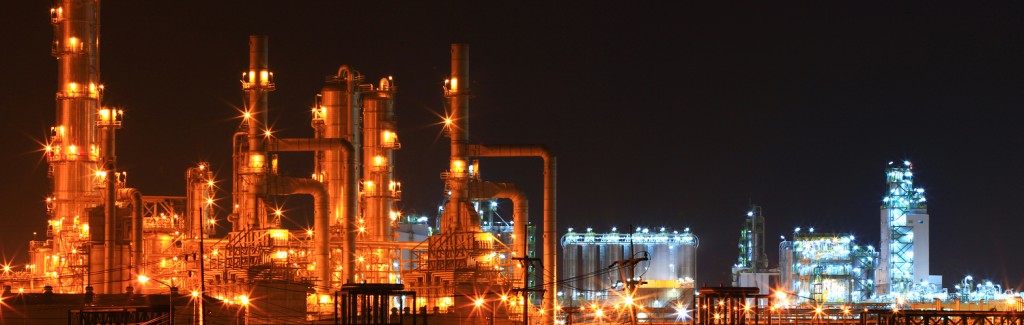
Finding Operational Efficiency atop the Chemical Manufacturing Supply Chain
Manufacturing chemicals for use in other industries could be rightfully described as the backbone of the U.S. gross domestic production. According to an American Chemistry Council report, 96 percent of all manufactured goods can be traced back to chemical manufacturers in one way or another. Such a ubiquitous industry comes with its fair share of responsibilities, as well as duties that can often clash with companies trying to optimize processes for enhanced production, streamlined operations and reduced costs. Chemicals sit so high on the supply chain, any efficiencies gained in these early stages have the potential to trickle down and empower other business associates.
But lean chemical manufacturing and meeting the needs of the manufacturing industry at large, don’t have to be mutually exclusive. Chemical manufacturing can support all the industries dependent on its services while still staying accountable to regulations and burgeoning industry trends.
“A balanced framework for delivery reduces a chemical manufacturer’s chances of overproduction.”
Environmental and operational sustainability through end-of-pipe treatment development
Applying lean best practices to eliminate operational waste can synchronize with end-of-pipe (EOP) waste reduction strategies. In the obvious sense, when a chemical manufacturer produces less waste as a byproduct of raw material creation, it may not necessarily indicate a drop in production. This change could just as easily demonstrate how chemical manufacturers have addressed operational deficiencies in their own processes which, when corrected, yield minimal waste. For example, companies that use the chemicals these manufacturers process won’t want a massive inventory cluttering their storage facilities, slowly expiring as the products go unused. Creating a balanced framework for delivery reduces a chemical manufacturer’s chances of overproduction, generating untenable amounts of waste for little discernible reason.
Another aspect of waste management in chemical processing is EOP treatment protocol, which has in the past gone to the wayside because of its perceived inability to add value to chemical manufacturing. Instead, as managerial mindsets swing further from environmental sustainability to fiscal solvency, EOP treatment became ancillary to production, an afterthought. However, with public opinion readjusting chemical manufacturing’s focus back on greener sensibilities, chemical manufacturers have had to concentrate on carving out justification for these important processing steps.
The truth is, enhancing EOP treatment has considerable benefit to businesses looking to improve on-site operations. According to a study from Malardalen University in Sweden, depending on the treatment processes already in place and planned for the future, chemical manufacturers can utilize technology capable of reclaiming waste materials for secondary use, reducing environmental waste, and uncapping material cost potential. Moreover, strengthened EOP treatment can act as insurance against downtime. As federal regulators crack down on chemical manufacturing to curb pollution rates, manufacturers who spend extra resources on waste treatment equipment may avoid costly shutdowns associated with a lax regard for the environment and safety.
“Granular data analysis is critical for seeding out and identifying operational shortcomings.”
Heightened efficiency through multifaceted data management
Chemical manufacturing already permeates nearly all areas of the industry. That said, there’s no glass ceiling on the potential for chemical manufacturing to continue effecting change on the larger American economic landscape. After all, we are talking about a more than $800 billion industry – so says the ACC – that not only supports almost every U.S. retailer, but contributes greatly to the expansion and modernization of American logistics and infrastructure as well.
With all these moving parts and fingers in proverbial soups, the potential for an individual manufacturer to compromise its own operations is quite high. For starters, since chemical manufacturing precedes the raw materials stage of many other manufacturer’s supply chains, these companies have the power to understand market volatility in areas like feedstock and energy better than their partners. Unfortunately, this can put undue stress on these same chemical companies to provide up-to-the-second price reporting for their own posterity, let alone others down their supply chains. With that in mind, discovering ways to integrate those financial data streams seamlessly into manufacturing processes also spurs valuable innovation in chemistry, essentially expanding scientific knowledge as a whole. The stakes are great, but the rewards are many.
Chemical manufacturing can support all the industries dependent on its services while still staying accountable to regulations and burgeoning industry trends.
Proactive data management for greater operational efficiency doesn’t end with mere price reporting, but extends out onto the plant floor. Recent research stated production variability for process chemicals experiences “extreme swings,” greater than many other manufacturing fields, and granular data analysis is critical for seeding out and identifying operational shortcomings. As an example, the organization followed a single unnamed chemical company as it attempted to deploy advanced “neural-network” data analytic strategies to study the impact of an array of environmental conditions – like temperature and coolant pressure – on yield sensitivity. After a thorough assessment, the chemical manufacturer was able to reduce both its raw materials waste and energy consumption by 20 and 15 percent respectively. To follow this one company’s example, chemical manufacturers will need to invest in the right kinds of equipment capable of deriving, auditing, and analyzing pertinent data to reach optimal efficiency.