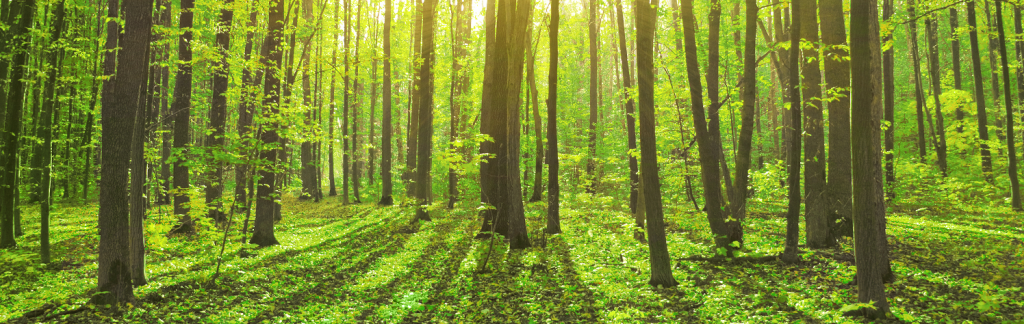
Efficiency in Pulp and Paper Mills
Achieving operational efficiency is essential in the pulp and paper industry. Variances in production can raise overhead costs and, in turn, make it more difficult to stay competitive in a global market. Fortunately, there are practical solutions that are often the result of smart planning and execution.
Cost and quality management in process industries
A recent whitepaper on operational efficiency in process industries, mentioned several challenges that manufacturers face when trying to improve operations. The pulp and paper industry, in particular, is under pressure to manage costs, quality and customer demands because of the nature of the market. As global demand for pulp and paper decreases over time, mills are required to grow more efficient and limit production variances as much as possible. Cost reduction and quality improvement are essential for industry players to remain competitive.
“Mills are required to grow more efficient and limit production variances as much as possible.”
Pulp and paper mills require smart planning and execution
One of the biggest obstacles in the efficiency of pulp and paper mills is the inability to achieve a high level of visibility and control of operations. If managers cannot measure, monitor and amend existing processes, efficiency in production is negatively affected. Cognizant points out that for an operation to be successful, it is essential to understand how equipment, technology and automation can improve existing operations. When considering two areas in need of constant attention – lowering operating costs and reducing process operations variability – planning and execution are paramount.
Cognizant noted that operational excellence and efficiency in production planning and manufacturing execution requires a solid link between the two. In production planning, schedules are required to be in sync with the demands of the entire supply chain. Accordingly, assets need to operate and be utilized at optimal levels. A big component in effective production planning is managing deviations between forecasts and planned deliveries. Successful manufacturing execution is dependent on the ability to adapt to schedule changes and manage unexpected issues as they arise. Any deviations in quality need to be addressed by analyzing and fundamentally understanding root underlying causes.
Identifying variability sources and applying solutions
In a blog post, Magnetrol International Incorporated indicated that level measurement is a critical part of improving efficiency in pulp and paper manufacturing operations. Pulp and paper mills have specific processes, such as chipping, pulping, washing and bleaching, which require specific knowledge, instrumentation and practical approaches. By looking at each process, determining sources of variability or deficiency, and applying solutions, facility-wide efficiency can be ascertained.
Magnetrol explained that pulp and paper mills are some of the largest industrial users of process water. As such, they are often located next to natural water sources and water levels of intake channels require constant monitoring. Outdoor conditions can sometimes cause complications for level controls, especially if accumulation of debris occurs. A solution for this problem is to install bar screens to remove debris that will damage mill equipment. Bar screens are routinely cleaned and raked, often through automatic level controls mounted in an upstream channel.
Equipment and Technology can Improve Efficiency in Mill Operations
Another possible issue that pulp and paper mills may need to address is the damage done to sensor equipment in the pulp digestion process. Heat and chemicals are used in combination to digest and transform wood chips into pulp by dissolving the base material. Due to high temperatures and harsh chemicals, sensors sometimes cannot withstand the conditions. Accordingly, it is helpful to instate continuous monitoring of overflow in order to avoid potential problems in pulp digesters.
Staying competitive in a global market
As the pulp and paper industry continues to strive for increased operational efficiency, planning and execution will continue play a fundamental role in cost and quality management. By limiting the amount of operational problems that occur throughout production, facilities have a chance to increase efficiency. In the case of source water and pulp digesters, understanding the cause of problems often leads to a quick and practical solution. While other areas of production may require more in-depth analysis, the planning and execution aspect will remain the same.