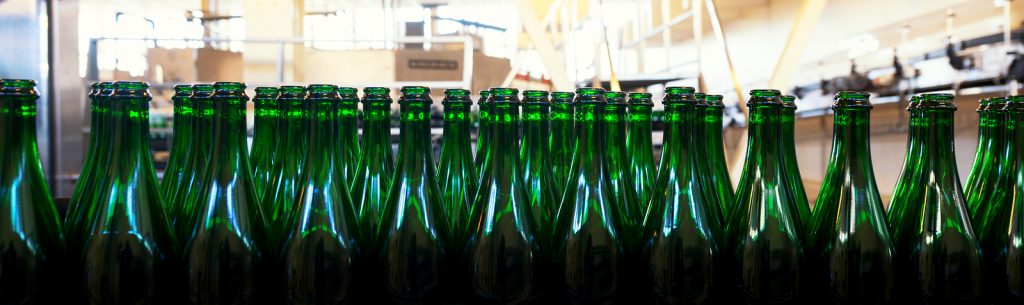
Glass Manufacturers See Through Energy Challenges
What challenges do glass manufacturers face as they attempt to reduce their energy consumption? Where might they turn to achieve significant results?
Troubles with energy efficiency in glass manufacturing as a sector, true to its product, are as transparent as they’ve ever been in this age of sustainability and eco-conscious private sector leadership. For the sake of the environment and operational costs, the glass industry has sought ways to rectify the matter.
Glass production: Portrait of an energy-intensive industry
According to data from the U.S. Energy Information Administration, glass manufacturing – the production of glass containers, flat glass, fiberglass, etc. – accounts for 1 percent of the U.S. manufacturing sector’s total energy consumption, placing it on par with other energy-intensive industries like steel and cement. However, as the EIA stipulates, glass manufacturing throughput volumes are much lower than others of its consumptive caliber, thus making it all the more inefficient in terms of energy use per unit.
“Melting processes consume 65% to 75% of energy required by glassmakers.”
Furnace operations represent the majority of energy expenses for glass manufacture across all subcategories, according to a study from the International Energy Agency. Depending on region of product, end product, and utilization of processes like sintering or cullet agglomeration, melting limestone, silica sand, or soda ash consumes anywhere from 65 to 75 percent of energy required by a given glassmaker. With so much riding on energy expended for direct production, any optimization efforts glass manufacturers undertake run the risk of compromising the integrity of the product and further complicate matters.
Nearly three-quarters of fuel usage for glass production in the U.S. relies on natural gas, with the final quarter primarily coming from electricity by way of “boosting.” In a pinch, electric boosting technology can increase production dramatically – but it comes at a cost to efficiency as manufacturers trade additional operating costs for immediate results to keep up with demand.
Although these challenges may be great, in what ways have some glassmakers already begun turning energy-intensive operations around?
Furnace upgrades and process changes retain heat and long-term value
Innovation will ultimately resolve the glass industry’s high energy consumption, especially as it pertains to the technology charged with controlling combustive fuels and heat transfer in glass-producing furnaces.
Glass manufacturing requires a light touch, both in forming products and controlling fuel.
First, any industry utilizing natural gas as a fuel source is bound to run into trouble with inconsistent diluent and hydrocarbon makeup. The result is an inability to predict or react to intensity increases or decreases within the burner, sometimes leading to resource overuse. Should glassmakers invest in technology capable of balancing the flow of natural gas into their furnaces regardless of composition or steading their air-to-fuel ratios, they will effectively reduce energy consumption at a traditionally wasteful process point.
Furthermore, while it may offer glass manufacturers greater market agility, electrical boosting technology can defeat its own purpose of meeting demand increases by adding considerably to energy costs, thus mitigating or negating revenue. Instead, the U.S. Department of Energy recommends outfitting outdated furnaces with waste heat capture retrofits for process heating. This technology captures lost heat and returns it to the furnace before electrical boosting occurs, priming the materials inside and reducing the amount of boosted energy required to raise the temperature to an actionable degree.
In fact, minimizing heat loss at any opportunity throughout the entire glass manufacturing process would also help immensely. Efficiency gains may only require operators to close furnace doors as often as possible or initiate a preventative maintenance program to ensure all energy-reliant assets stay in good working order. Never underestimate these little optimizers – they can really make a difference.